
Bacteria can also enter the water when mold tools are changed. Semi-closed loops usually have open or loosely covered sumps that allow bacteria to enter the water. It is rarely practical or cost-effective to eliminate all bacteria from a recirculating water system. For plastic injection molders, the mold tool is the worst place for corrosion by-products to build up. Corrosion causes iron and other metals to accumulate in the water and inadequate water treatment can allow those corrosion by-products to accumulate and lead to fouling on heat exchange surfaces.įouling insulates heat transfer and leads to increased Cycle Time. A good water treatment program can minimize the effects of corrosion, but not stop it completely. Virtually all recirculating water systems contain some steel components. Multiply that number by ten and compare it to your system volume. Add in cleaning and flushing of the water attachment manifold (you do flush the water manifold before connecting the new, clean mold, right?) and any other cleaning and maintenance practices that include water replacement. Figure out how much water your mold tools hold, then multiply that volume by the number of mold changes you make each year. Most plastic injection mold loops lose significantly more than 10% of their volume when mold tools are changed. Learn More About Our Closed Loop Services My System Has A Closed Loop - Why Does It Lose Water?ĪSHRAE defines a “closed loop” as a system that loses less than 10% of its volume annually. Scale the thickness of a human hair can result in a 20% loss of heat exchange efficiency and that translates directly to increased Cycle Time.
PELLUCID WATER SKIN
Mold surfaces are generally the hottest point in the system and high skin surface temperatures are prone to scale precipitation. How Can Scale Form In A Closed Loop?Ĭlosed loops rarely have scale problems, but mineral scale can form in systems with high hardness and alkalinity make-up sources. Proper cleaning, layup and maintenance practices can completely prevent increased Cycle Time problems. This results in increased Cycle Time which in turn results in higher operating costs and lower output of the machine. The heat transfer capacity of the mold tool is reduced if scale, corrosion by-products or biofilm accumulate on the waterside of the mold. The Cycle Time for each part depends on a number of design parameters including the flow rate and heat transfer capacity of the mold tool.
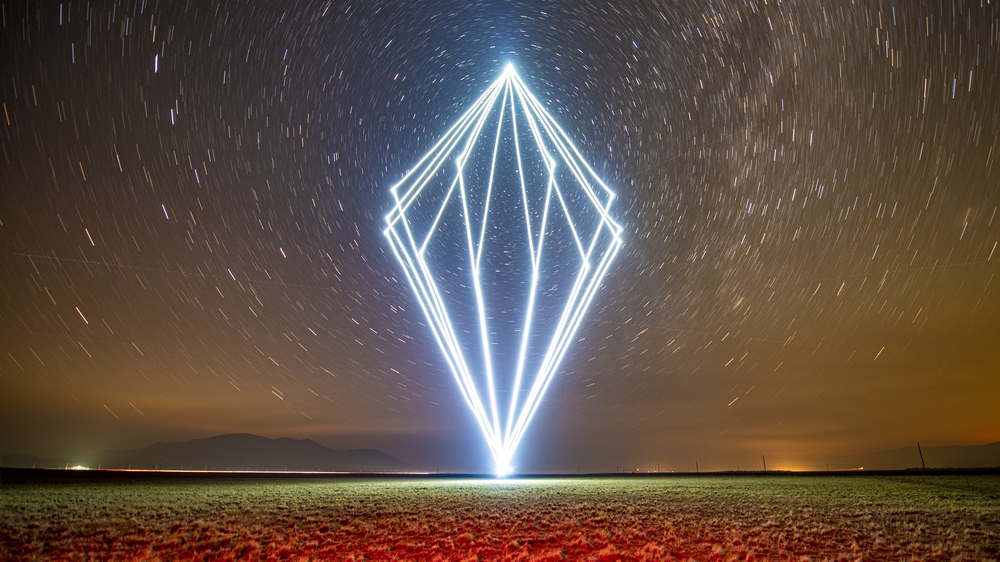
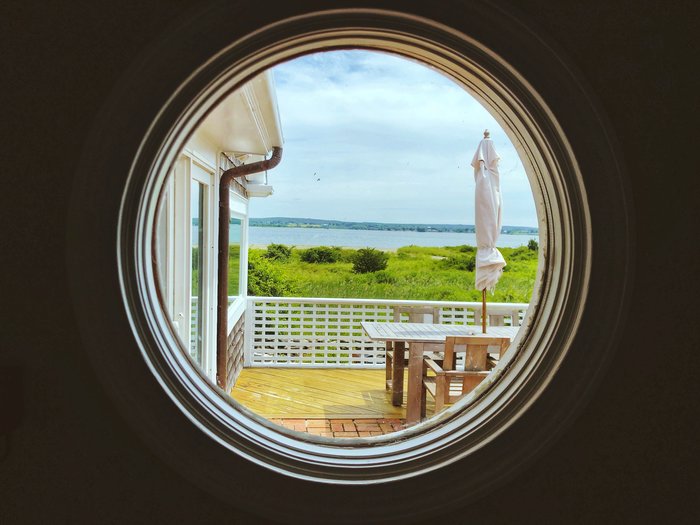
The time it takes between new parts coming out of the mold is referred to as Cycle Time. These ports in the mold tool are engineered to optimize the flow of water so that the plastic cools enough to allow the newly molded part to come out of the mold as a solid object. Cooling water flows through holes and channels drilled and cut in the mold tool. Water is used to cool and remove heat from the liquid plastic once it fills the mold. Why Is It Important To Clean And Lay Up My Mold Tools?
